Noch mehr Wissen in unseren REMIRA Whitepapern
In unseren Whitepapern erhalten Sie nützliche Praxistipps rund um die Themen Supply Chain und Omnichannel Commerce.
.jpg)
Integriertes Sales & Operations Planning
Kostenlos anfordern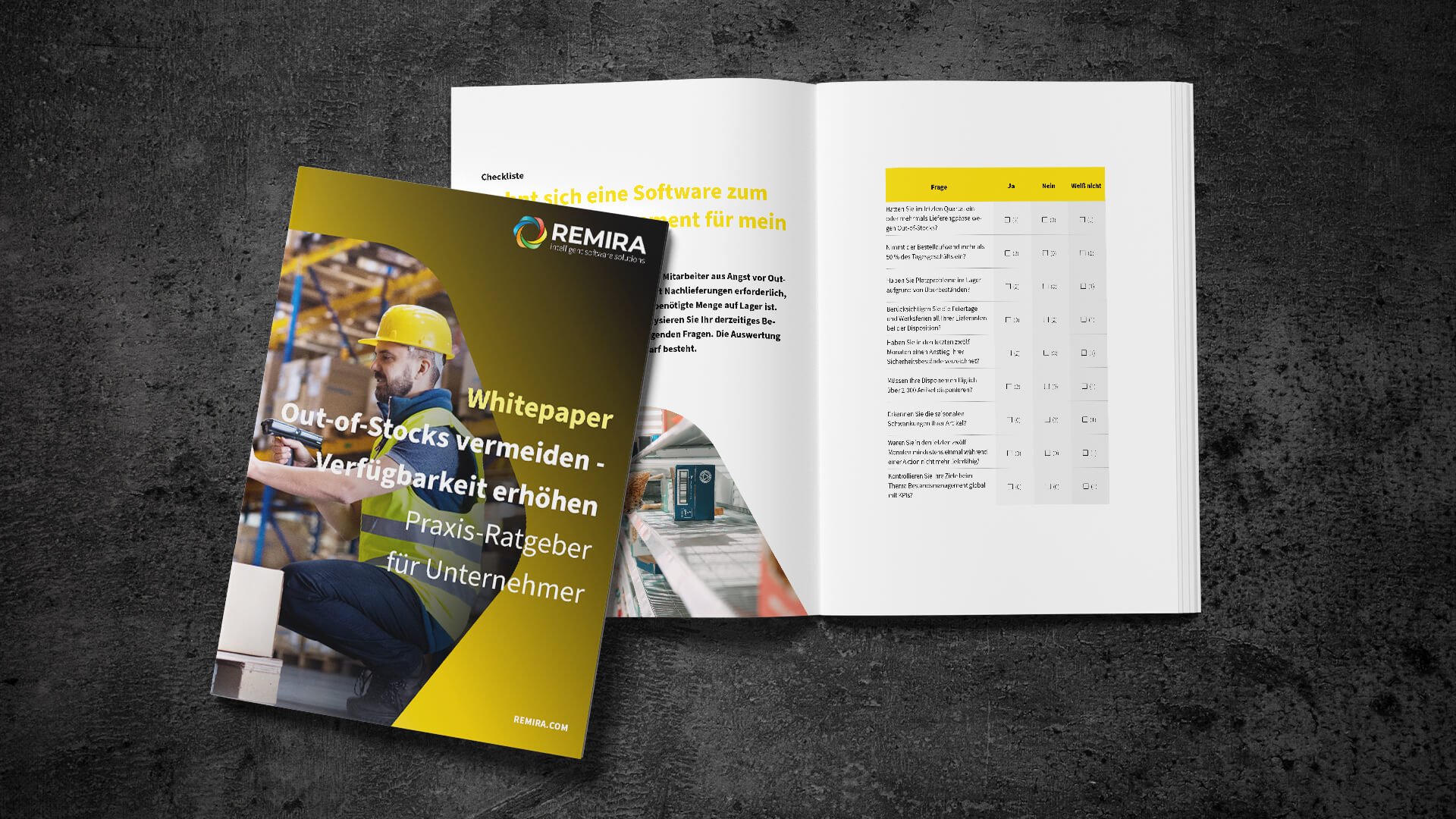
Out-of-Stocks vermeiden - Verfügbarkeit erhöhen
Kostenlos anfordern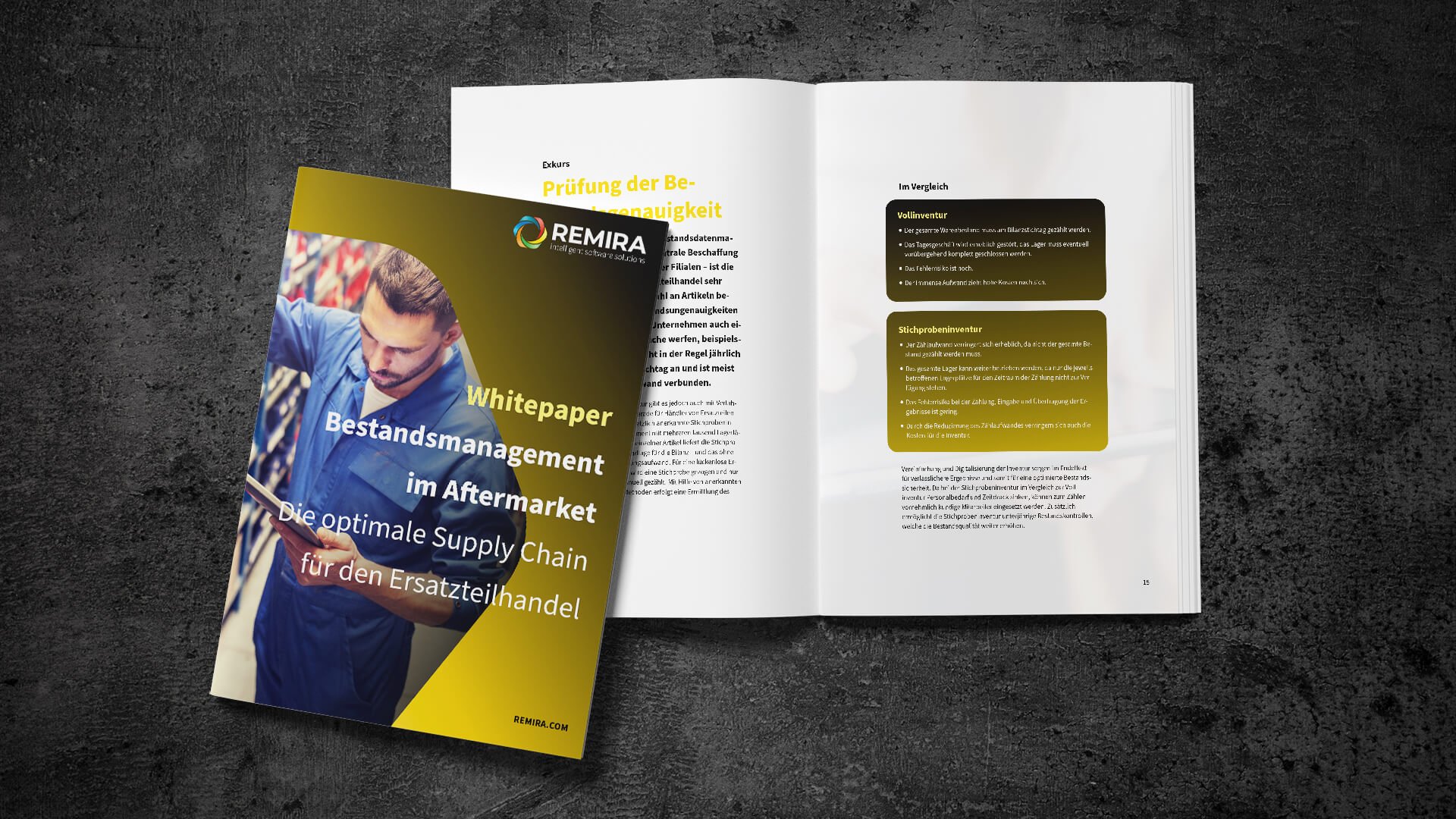
Die optimale Supply Chain für den Ersatzteilhandel
Kostenlos anfordern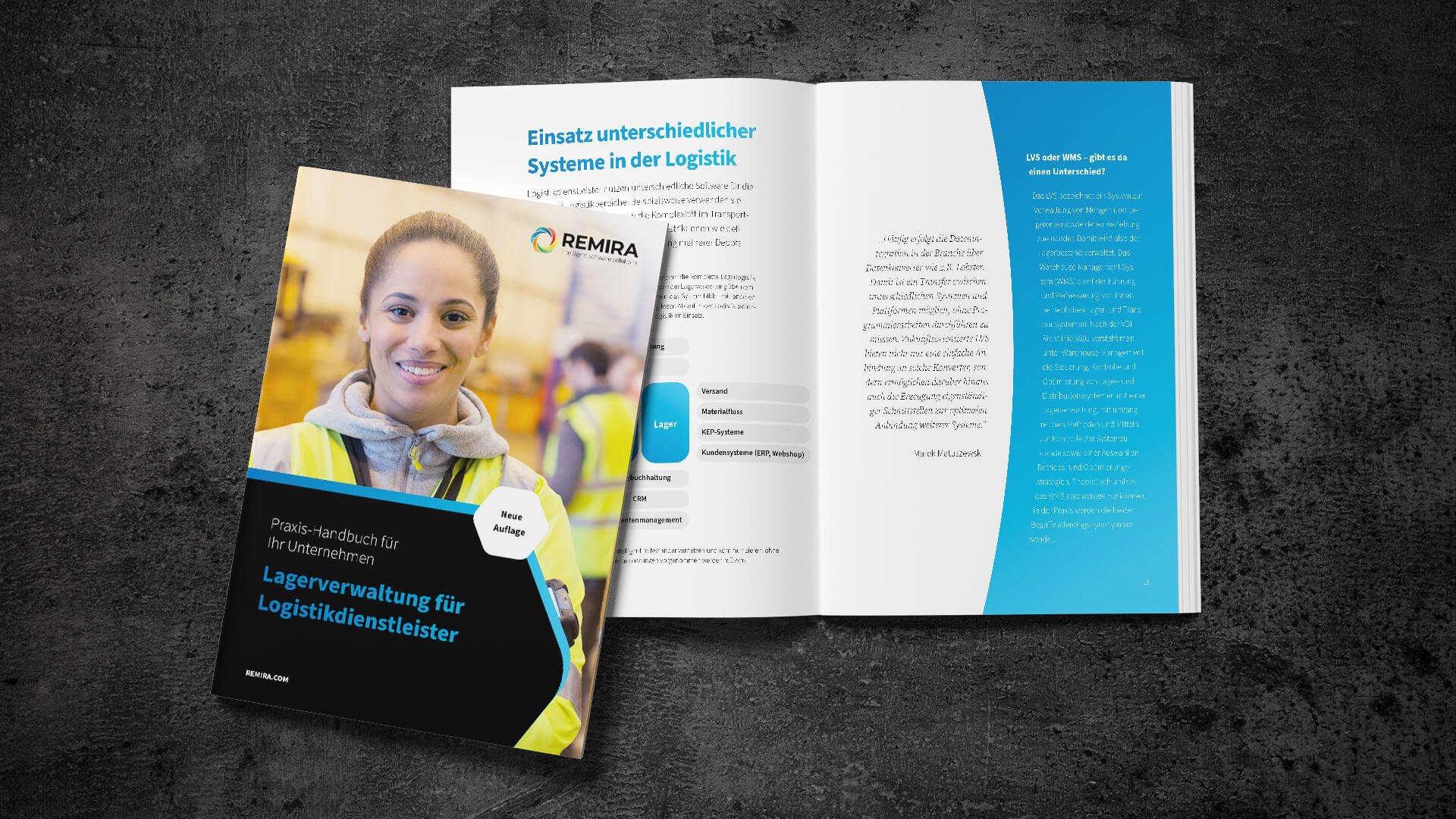
Lagerverwaltung für Logistikdienstleister
Kostenlos anfordern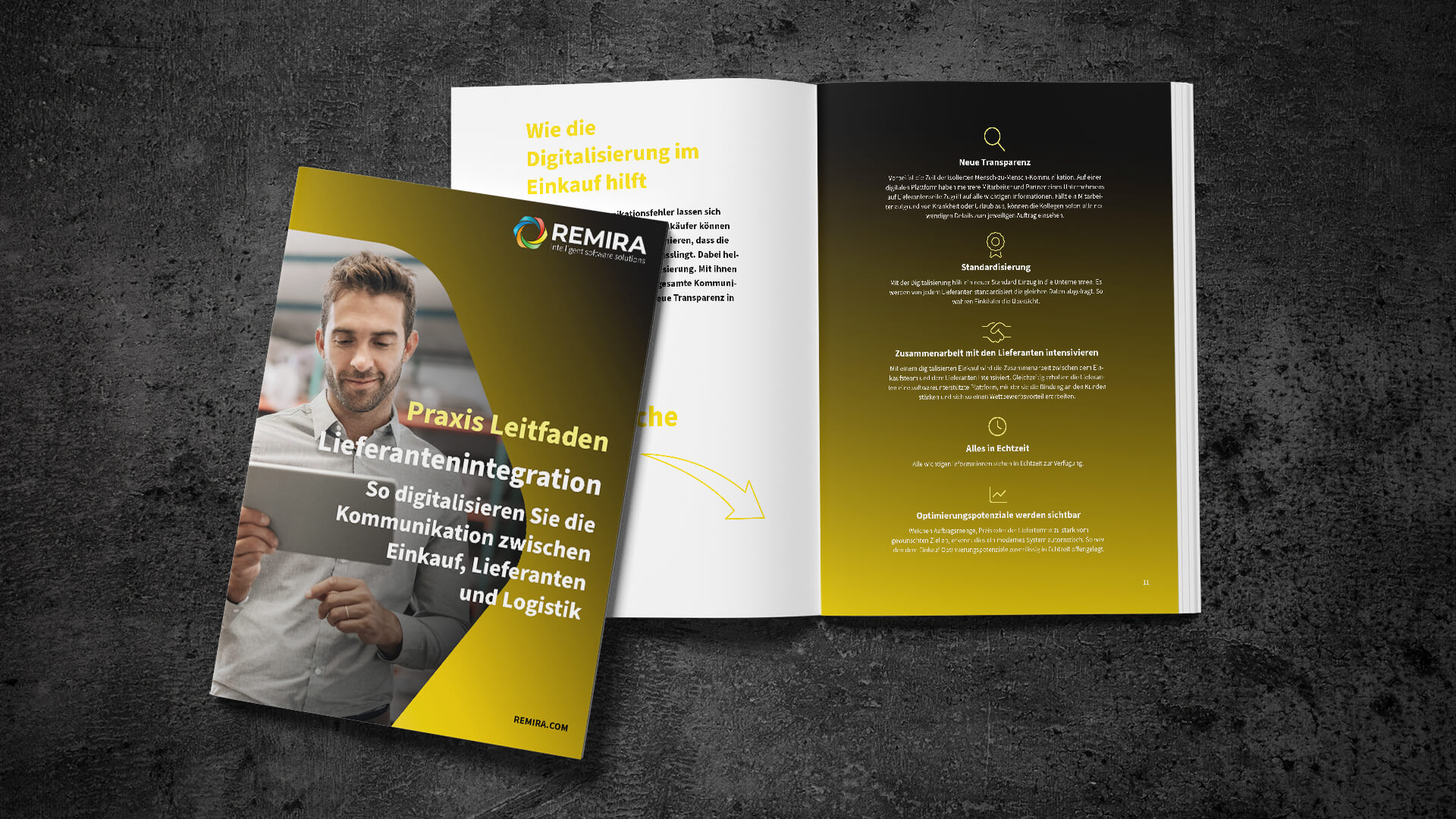
Leitfaden Lieferantenintegration
Kostenlos anfordern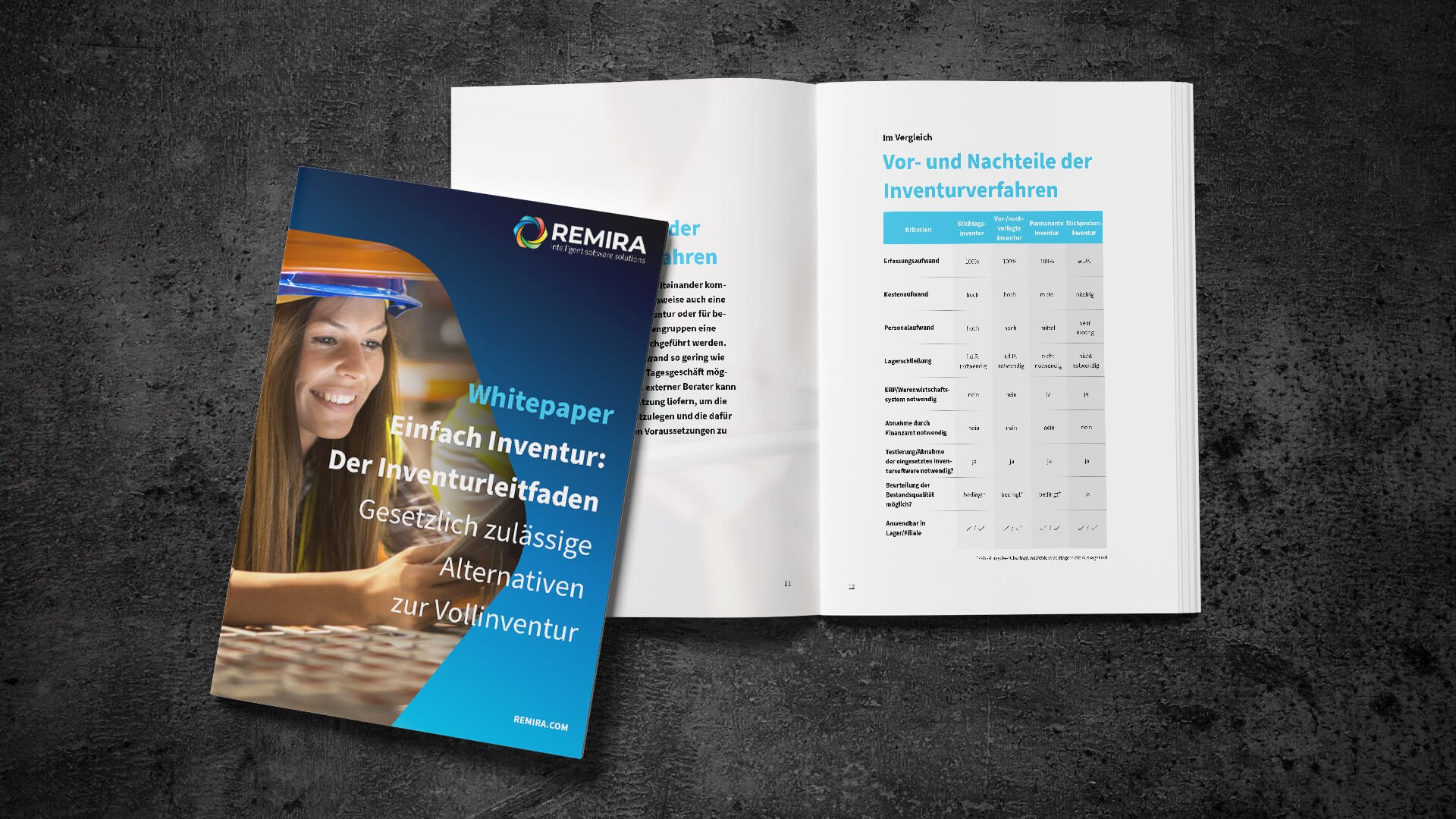
Einfach Inventur: Der Inventurleitfaden
Kostenlos anfordern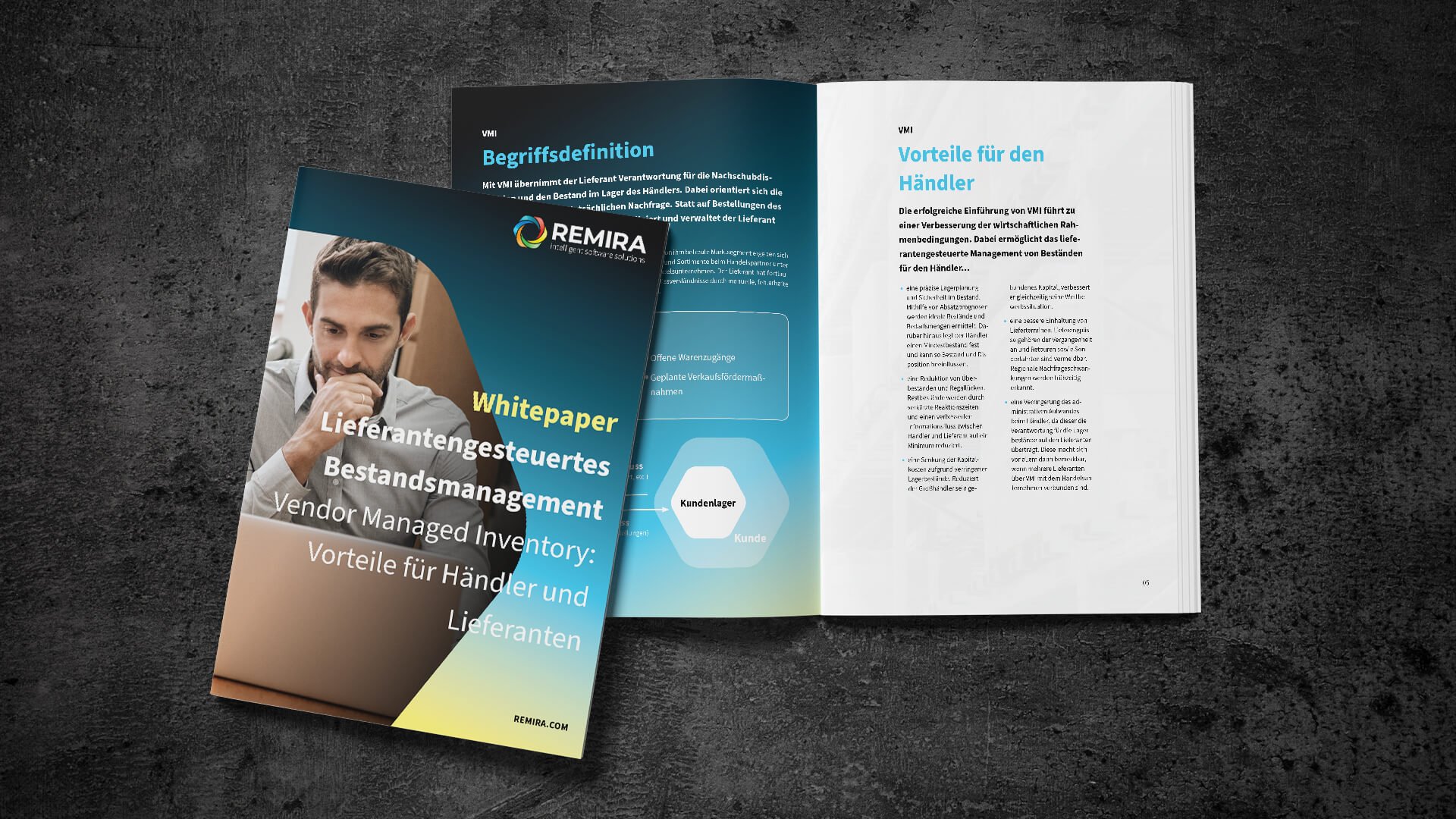
Vendor Managed Inventory: Vorteile für Händler und Lieferanten
Kostenlos anfordern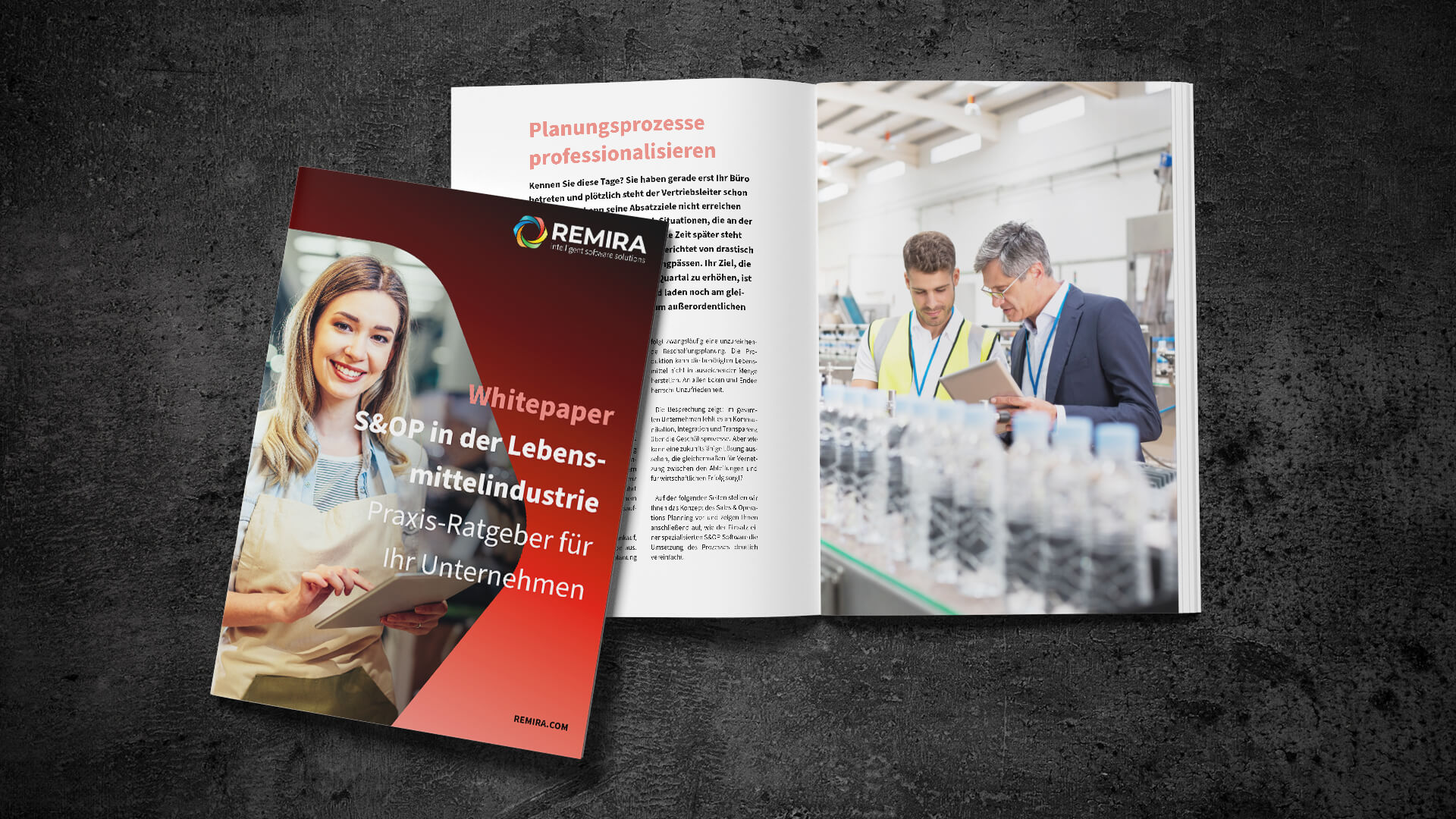
S&OP in der Lebensmittelbranche
Kostenlos anfordernAlle Glossar-Begriffe
Advanced Planning and Scheduling
API
APS
Artikelnummer
ASIN
Auftrag
Auftragsabwicklung
Auftragsdurchlaufzeit
Auftragsfertigung
Augmented Reality
Auslagerung
AutoStore
Avisierung
B2B und B2C
Bedarf
Belegausgabepflicht
Beleglose Lagerführung
Beschaffung
Beschaffungslogistik
Beschaffungsmanagement
Beschaffungsplanung
Best-of-Breed
Bestand
Bestandscontrolling
Big Data
Blockchain
Bottom-Up Planung
Buy Box
Category Management
Chaotische Lagerhaltung
Charge
Click and Collect
Click and Reserve
Cloud Commerce
Corporate Social Responsibility
Curated Shopping
Curbside Pick-up
Customer Experience Management
Customer Journey
Customer Relationship Management (CRM)
Data Warehouse
Digital Commerce
Digital Signage
Direct-to-Consumer (D2C)
Disponent
Distributionslager
Distributionslogistik
Dropshipping
DSFinV-K
Durchlaufregal
E-Procurement
EAN
EDI Clearing Center
EDIFACT
Endless Aisle
Exoskelett
Fahrerloses Transportsystem (FTS)
Fast Moving Consumer Goods (FMCG)
FEFO
FIFO
Fiskalisierung
Fiskalspeicher
Flottenmanagement
Flurförderfahrzeug
Fourth Party Logistics - 4PL
Frontend
Gamification
Gebinde
Gegenstromverfahren
Geschenkbon
GoBD
Green Logistics
GTIN - Global Trade Item Number
Handelslogistik
HIFO
Integrated Business Planning (IBP)
Integrierte Planung
Internet of Things (IoT)
Intralogistik
Inventursoftware
Inventurverfahren
IWD PS 880
Kassensicherungsverordnung (KassenSichV)
Kaufentscheidung
Key Performance Indicator (KPI)
KMU
Kommissioniermethoden
Kommissionierverfahren
Kommissionierlager
Konsignationslager
Kontraktlogistik
Kuppelproduktion
Künstliche Intelligenz
Ladeeinheit
Ladehilfsmittel
Lager
Lagerarten
Lagerbestand
Lagerhaltung
Lagerhaltungskosten
Lagerkennzahlen
Lagerlogistik
Lagerverwaltungssystem
Lebensmittellogistik
Lieferantenintegration
Lieferfähigkeit
Lieferkettengesetz
Liefertreue
LIFO
LOFO
Logistik und ihre Teilbereiche
Losgrößen
Management by Exception
Maschinelles Lernen
Materialfluss
Materialwirtschaft
Maximalbestand
MDE-Gerät
Meldebestand
Micro-Hub
Mindestbestand
Mindesthaltbarkeitsdatum (MHD)
Mobile Commerce (M-Commerce)
Mobile Datenerfassung
Mobile Kasse
mPOS (Mobile Point of Sale)
Multichannel
Nullbon
Omnichannel
Omnichannel Commerce
Order Management
Order Management System (OMS)
Palette
Payment Provider
Permanente Inventur
Pflichtenheft
Pick-by-Cart
Pick-by-Light
Pick-by-Paper
Pick-by-Scan
Pick-by-Voice
Pick-by-Watch
Planogramm
POS (Point of Sale)
Procurement Software
Product Experience Management (PXM)
Product Lifecycle Management (PLM)
Produktinformationsmanagement (PIM)
Produktionslogistik
Push & Pull
Quick Commerce
Radio Frequency Identification (RFID)
Recommendation Engines
Regalplanung
Repricing
Responsive Design
Ressourcenmanagement
Retail
Retoure
Retourenmanagement
Return-in-Store
ROPO-Effekt
Self-Checkout
SGTIN
Ship-from-Store
Showrooming
Sicherheitsbestand
Social Commerce
Software
Software-as-a-Service (SaaS)
Space Management
Stationärer Handel
Streuverlust
Stückgut
Stückliste
Supplier Relationship Management (SRM)
Technische Sicherungseinrichtung (TSE)
Top-Down Planung
Transportlogistik
Transportmanagement
TUL-Prozesse
Umlagerung
Umschlagslager
Umschlagslogistik
Unified Commerce
Unternehmenslogistik
Virtuelles Lager
Voice Commerce
Vor- und nachverlegte Inventur
Vorratslager
Warehouse Management System
Warenausgang
Warendisposition
Wareneingang
Warenwirtschaftssystem
Wiederbeschaffungszeit
Zeitfenstermanagement
Zentrallager
Zulieferer
Zwischenlager