Pick-by-Paper
Pick-by-Paper ist ein Begriff aus der Logistik. Es beschreibt ein mögliches Verfahren der Kommissionierung. Diese Kommissioniermethode kommt ohne jegliche elektronischen Hilfsmittel aus, da für hierbei nur eine ausgedruckte Pick- oder Kommissionierliste genutzt wird.
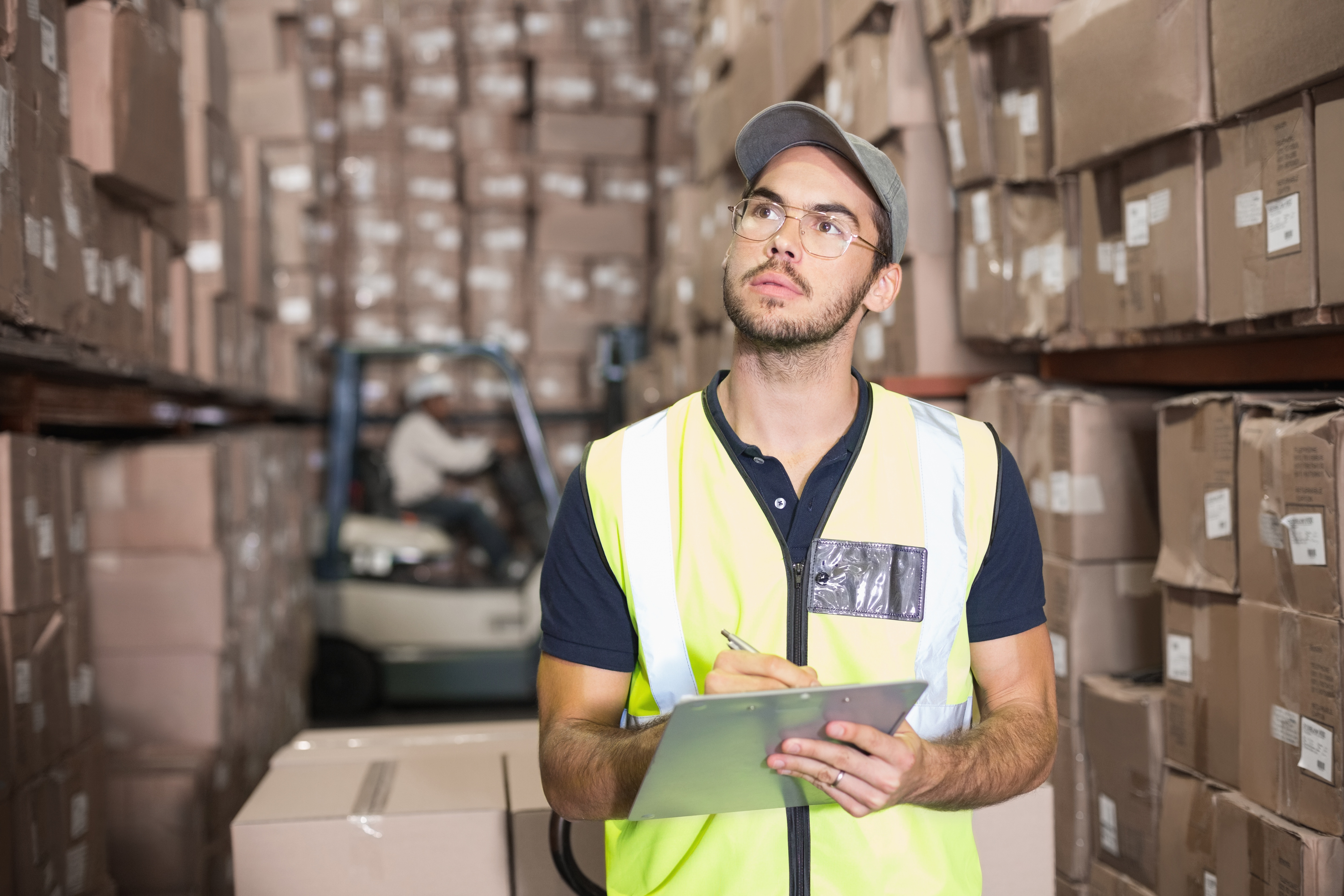
Erklärung des Pick-by-Paper Verfahrens
Bei dem Pick-by-Paper Verfahren handelt es sich um das klassische Kommissionierverfahren in der Logistik. Es bildet sozusagen die Grundlage aller Kommissioniermethoden. Der Begriff Kommissionierung beschreibt in der Logistik ein Verfahren, bei dem Waren und Güter aus dem Gesamtsortiment für einen Auftrag zusammengestellt werden. Bei dem Verfahren "Pick-by-Paper" erhält der Mitarbeiter für jeden Auftrag eine Pickliste, auch Pickzettel genannt. Auf dieser Liste sind alle Artikel eines Auftrages, sowie deren Artikelnummer, die erforderliche Menge und deren Lagerort verzeichnet. Die Pick-by-Paper-Methode kommt dementsprechend ohne technische Hilfsmittel aus.
Pick-by-Paper wird auch beleghafte Kommissionierung genannt, da sämtliche Arbeitsschritte schriftlich dokumentiert werden. Auf dem Pickzettel werden nicht nur die einzelnen Waren, die entnommen wurden, abgehakt, sondern es werden auch fehlerhafte Lagerbestände und ähnliches vermerkt. Der Pickzettel dient später als Beleg für die Übertragung aller Angaben in das Lagerverwaltungssystem (Warehouse Management System) oder in das ERP-System.
Die Pick-by-Paper Methode eignet sich wegen ihrer kostengünstigen Integration und einfachen Steuerbarkeit vor allem für kleine und mittelständische Unternehmen. In solchen Unternehmen steht die aufwändige Einführung von beleglosen Kommissioniermethoden, wie Pick-by-Light, Pick-by-Vision oder Pick-by-Scan, und den damit verbundenen Kosten nicht im Verhältnis zu den Vorteilen, die diese beleglosen Methoden mit sich bringen. Auch für Unternehmen mit überschaubaren Lagern und niedrigen Umschlagszahlen eignet sich die Pick-by-Paper Methode. Für Unternehmen mit großen Lagern, hohen Umschlagszahlen oder starkem Wachstum sind jedoch die technischen, beleglosen Kommissionierverfahren eine effizientere Strategie für die Bearbeitung von Aufträgen.
Wie läuft das Pick-by-Paper Verfahren typischerweise ab?
- Eine Bestellung wird von einer internen Abteilung, zum Beispiel der Produktion, oder von einem Kunden aufgegeben. Diese wird nach ihrem Eintreffen von der Lagerverwaltung überprüft,
- Daraufhin wird der Pickzettel erstellt. Hierfür kopiert die Lagerverwaltung entweder die Bestellung oder stellt den Pickzettel mithilfe eines Systems zusammen. Die Lagerverwaltung überprüft, dass vor allem die wichtigen Informationen zur Art und Mange der Ware sowie zum Lagerort auf dem Pickzettel verzeichnet sind.
- Der Pickzettel wird dann an das Team der Kommissionierung weitergeleitet, welche diesen dann an einen Mitarbeiter vergibt.
- Der Kommissionierer lokalisiert die Ware im Lager und entnimmt die angegebene Ware aus dem Lagerort.
- Nach der Entnahme hakt der Mitarbeiter die Position auf dem Pickzettel ab. Wenn die Ware beschädigt oder nicht auffindbar ist, wird dies auf dem Pickzettel vermerkt.
- Wenn der Auftrag fertigzusammengestellt wurde, muss der Kommissionierer alle Schritte manuell in das Lagerverwaltungs- oder ERP-System übertragen.
Die Weiterentwicklung: Pick-by-Tablet-Verfahren
Eine Weiterentwicklung des des Pick-by-Paper Verfahrens ist das Pick-by-Tablet Verfahren. Hierbei dient ein Tablet als Pickzettel. Durch die Digitalisierung des Pickzettels entfällt vor allem die nachträgliche, händische Übertragung der Daten in das jeweilige System. Bei der Pick-by-Tablet Methode handelt es sich dann bereits um eine Art der beleglosen Kommissionierung, da eine mobile Datenerfassung vorliegt. Jedoch handelt es sich immer noch um eine eher manuelle Kommissioniermethode, da der Mitarbeiter die Entnahme auf der Pickliste auf dem Tablett abhaken muss.
Vorteile und Nachteile des Pick-by-Paper Verfahrens?
In wirtschaftlicher Hinsicht bietet das Pick-by-Paper Verfahren für kleine und mittelständische Unternehmen und Start-Ups einige Vorteile. Jedoch ist es gerade bei modernen Just-in-Time-Produktionen weniger bis gar nicht rentabel, da es in Bezug auf Effizienz, Fehlerquote und Skalierung der Warenzusammenstellung Nachteile birgt.
Das Kommissionierverfahren mit einem Pickzettel bietet folgende Vorteile:
- Keine bis geringe Investitions- und Anschaffungskosten
- Kaum Schulungsaufwand
- Flexible Erweiterungsmöglichkeiten
- Einfache Steuerbarkeit
- Schnelle Einarbeitungszeiten
- Keine Wartung technischer Geräte
Das Pick-by-Paper Verfahren birgt aber auch einige Nachteile:
- Mehrfache Datenerfassung
- Tendenziell hoher Fehleranfälligkeit
- Eingeschränkte Beweglichkeit der Mitarbeiter, da sie immer mindestens eine Hand für den Pickzettel brauchen
- Mitarbeiter des Kommissionierungsteams müssen sich im Lager sehr gut auskennen.
- Intransparente Arbeitsweise, da Daten manuell erfasst werden
- Großer Verwaltungsaufwand durch die manuelle Dateneingabe
- Hoher Papierverbrauch
Obwohl das Verfahren durchaus Vorteil aus Produktivitäts- und vor allem Kostensicht hat, ist dieses in der heutigen, digitalisierten Welt nicht mehr zeitgemäß. Bei dem heute üblichen, schnellen Warendurchlauf ist vor allem die digitale Erfassung der Daten für das gesamte Unternehmen von hoher Bedeutung.
Alternative Kommissioniermethoden
- Pick-by-Scan: Das Verfahren "Pick-by-Scan" ist die wohlbekannteste Form der beleglosen Kommissionierung. Der Kommissionierer nutzt anstelle eines Pickzettels ein MDE-Gerät, welches mit einem Touchscreen und einer Scanfunktion ausgestattet ist. Mit dem Scanner werden alle Warenentnahmen in Echtzeit vom System erfasst, sodass vor allem die Bestandsänderung direkt im System abgespeichert werden kann.
- Pick-by-Voice: Das Kommissionieren kann auch mit einem sprachbasierten System unterstützt werden. Dieses System nennt man auch Pick-by-Voice Verfahren. Bei diesem findet die Kommunikation zwischen dem Kommissioniersystem und dem Kommissionierer mittels Spracheingabe und -ausgabe statt.
- Pick-by-Light: Das Pick-by-Light-System nutzt Signalleuchten und elektronische Fachanzeigen. Das System wird Pick-by-Light genannt, da dem Kommissionierer über Signalleuchten zum richtigen Entnahmefach geleitet wird. Direkt vor Ort wird dem Mitarbeiter über die elektronische Fachanzeige angezeigt, welche Artikel in welcher Menge er entnehmen soll. Durch das Bestätigen der Entnahme über eine Quittiertaste werden die Informationen an des Lagerverwaltungssystem übermittelt.
- Pick-by-Vision: Bei diesem Kommissionierverfahren trägt der Kommissionierer eine Datenbrille. Dieses Verfahren wird auch Augmented Realtiy unterstützte Kommissionierung genannt. Über die Brille werden mithilfe von WLAN-Technik die wichtigen Informationen für die Kommissionierung direkt im Blickfeld des Kommissionierers angezeigt. Es ist teilweise auch möglich, über die Brillen den kürzesten Weg zum Lagerplatz anzuzeigen. Ein Trackingsystem erfasst die Position des Kommissionierers.
- Pick-by-Point: Bei der Kommissioniermethode Pick-by-Point wird den Kommissionierer mithilfe von Lasern, die an den Regalgängen installiert werden, der Weg zu der zu entnehmenden Ware angezeigt. Dieses Verfahren kann mit dem Pick-by-Paper-Verfahren oder einem Pick-by-Terminal Verfahren kombiniert werden.
- Pick-by-Terminal: Hierbei handelt es sich um eine weiteres Verfahren der beleglosen Kommissionierung. Die Kommunikation mit dem Kommissionierer erfolgt anhand eines fest installierten Terminals. Die Terminals können auch an Gabelstaplern oder anderen Kommissionierfahrzeugen angebracht werden. Die Erfassung erfolgt über einen Scanner.
- Pick-by-RFID: Bei einem Kommissionieren nach der RFID (Radio Frequency Identification) Methode, wird die RFID-Technik genutzt, um Artikel während des gesamten Kommissionierungsprozesses im Lager zu verfolgen. Der Kommissionierer erhält seine Aufträge direkt auf dem RFID-Gerät, wird von diesem geleitet und kann die entsprechenden Artikel aus dem Regal entnehmen.