Noch mehr Wissen in unseren REMIRA Whitepapern
In unseren Whitepapern erhalten Sie nützliche Praxistipps rund um die Themen Supply Chain und Omnichannel Commerce.
.jpg)
Integrated Sales & Operations Planning
Our whitepaper "Integrated Sales & Operations Planning" shows you how to use the strategic approach of S&OP to network sales, production, and purchasing planning and other corporate areas, and how to use a coordinated process to create a valid database for making business decisions quickly.
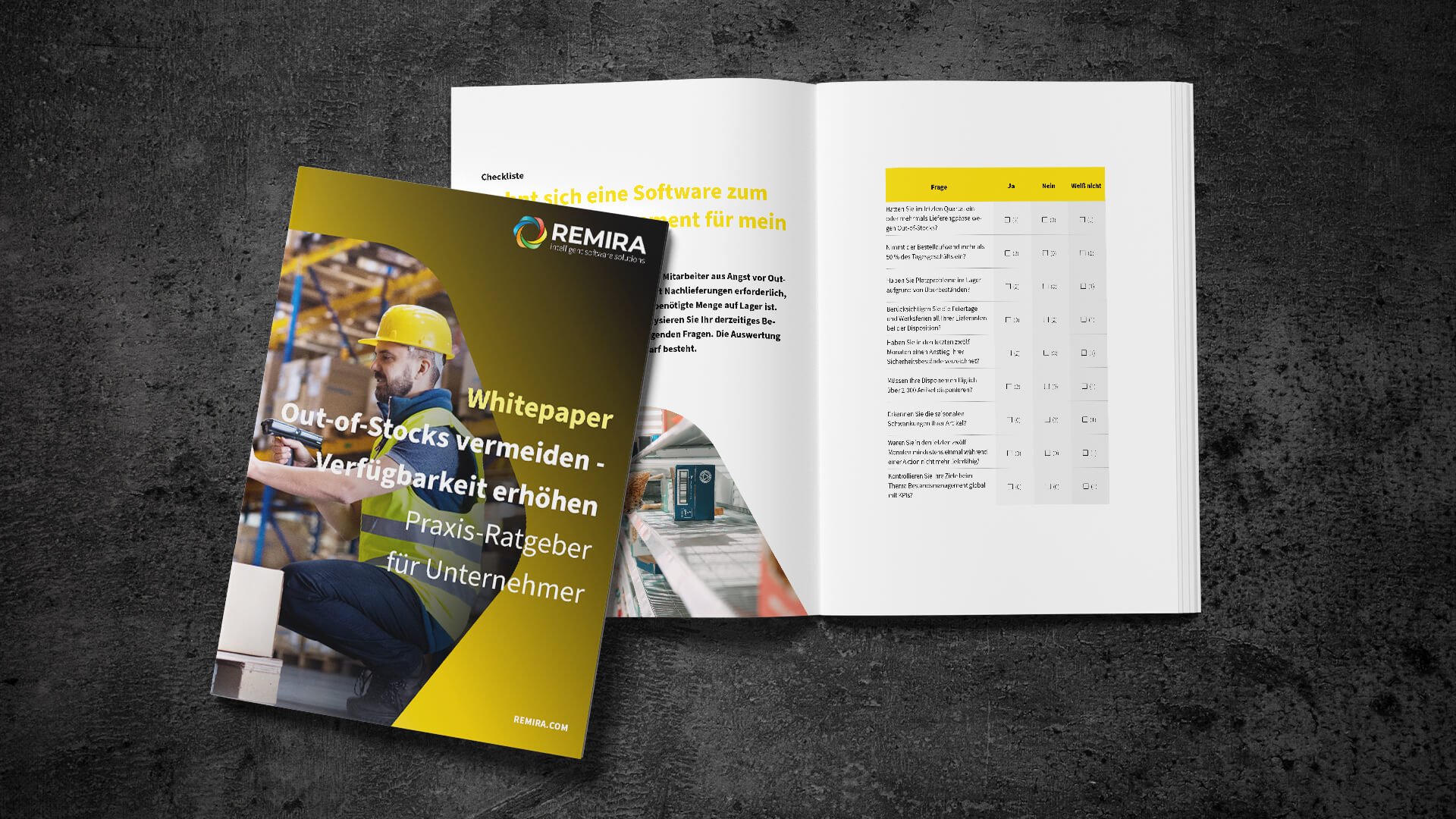
Avoid Out-of-Stock - Increase Availability
The REMIRA white paper "Avoide Out-of-Stocks - Increase Availability" shows why inventory management is an important competitive factor, how digital inventory management can be introduced during ongoing operations, and why it quickly provides significant savings.
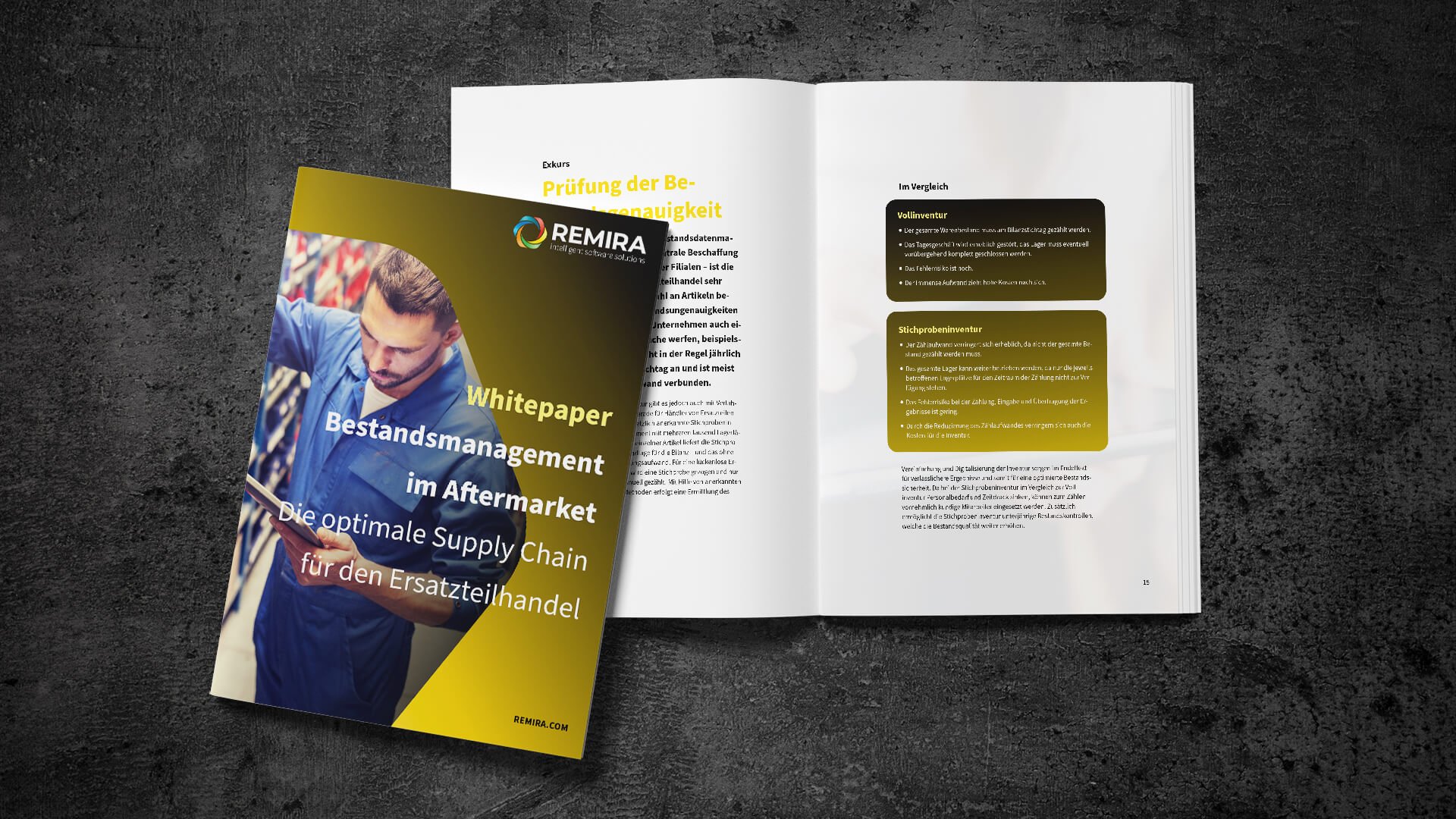
The Optimal Supply Chain for the Spare Parts Trade
The REMIRA white paper "The optimal supply chain for retailers" shows the challenges for dealers in the aftermarket and provides assistance for optimizing the supply chain. It also shows the most important aspects you need to consider as a spare parts dealer and how you can always determine the optimal demand and ensure high availability with the help of artificial intelligence.
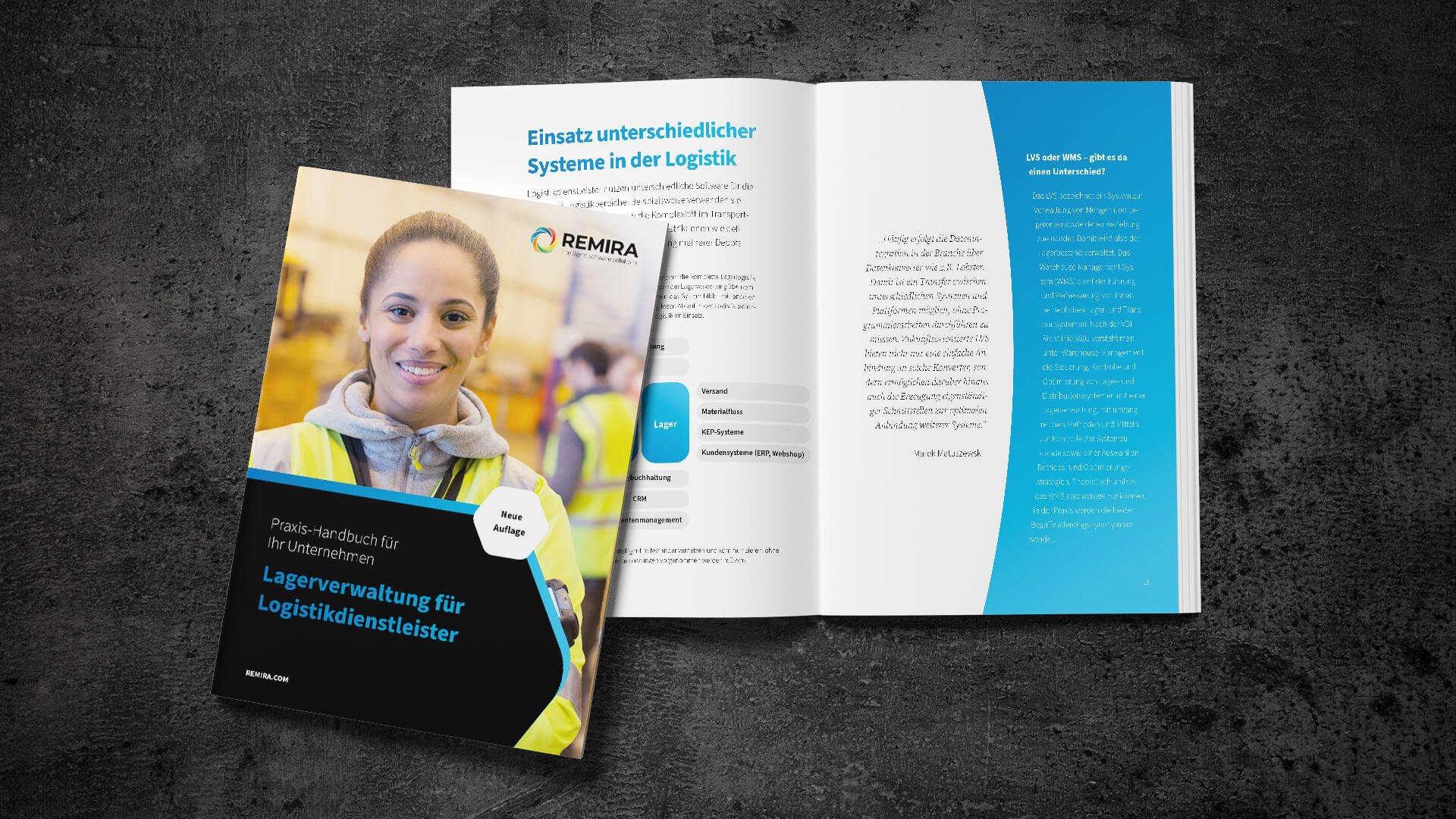
Warehouse Management for Logistics Service Providers
In our whitepaper "Warehouse Management for Logistics Service Providers", we explain how you can easily manage complex warehouse processes, which systems are used in logistics and give you practical help in selecting a warehouse management system.
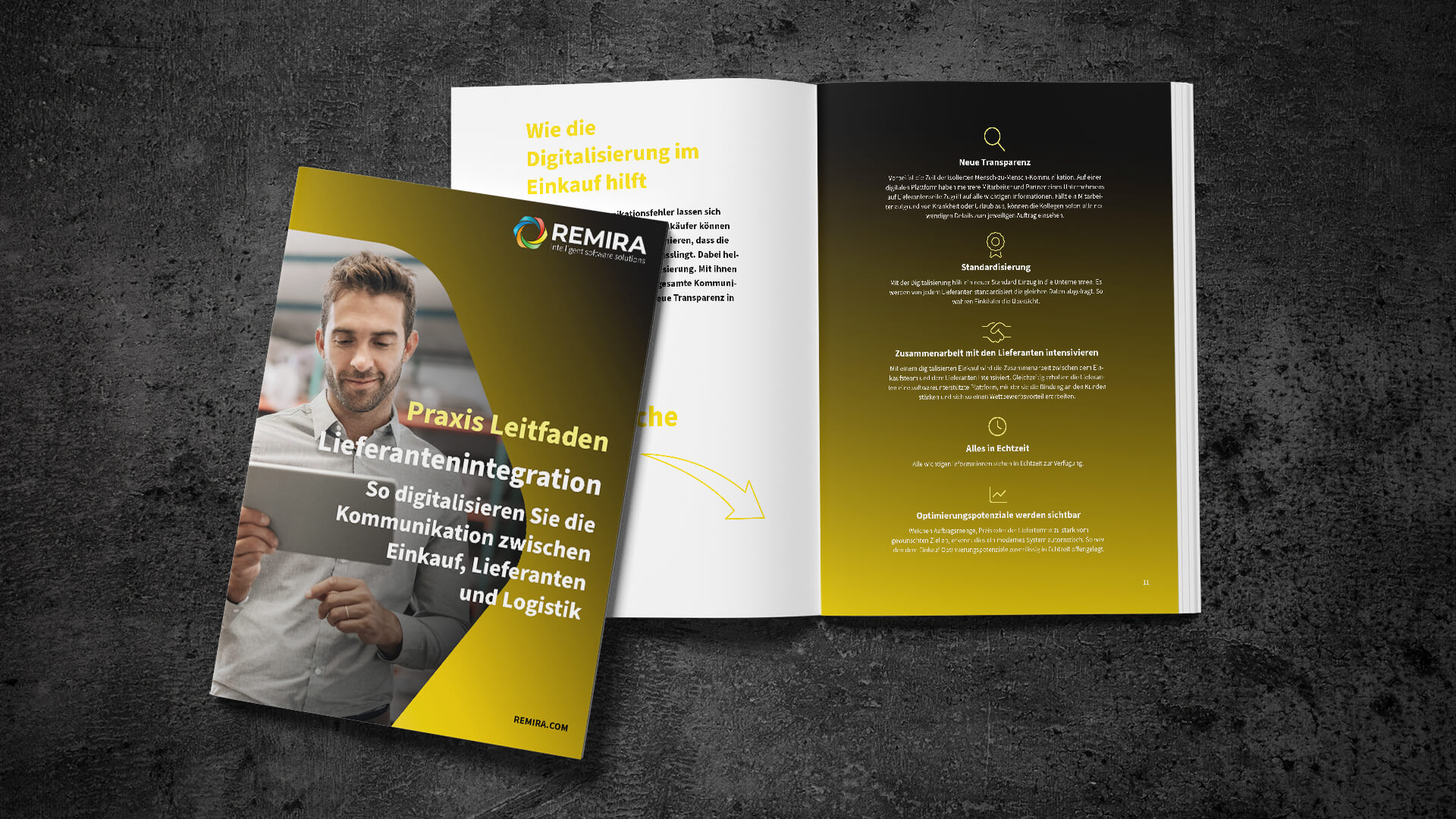
Supplier Integration Guide
Our whitepaper "Supplier Integration Guide" shows the opportunities and benefits of digital procurement. You will get practical assistance on the way to digitizing your procurement and learn which processes you can already digitize today without much effort. We also show you how you can also integrate smaller suppliers into the processes - with or without an EDI project.
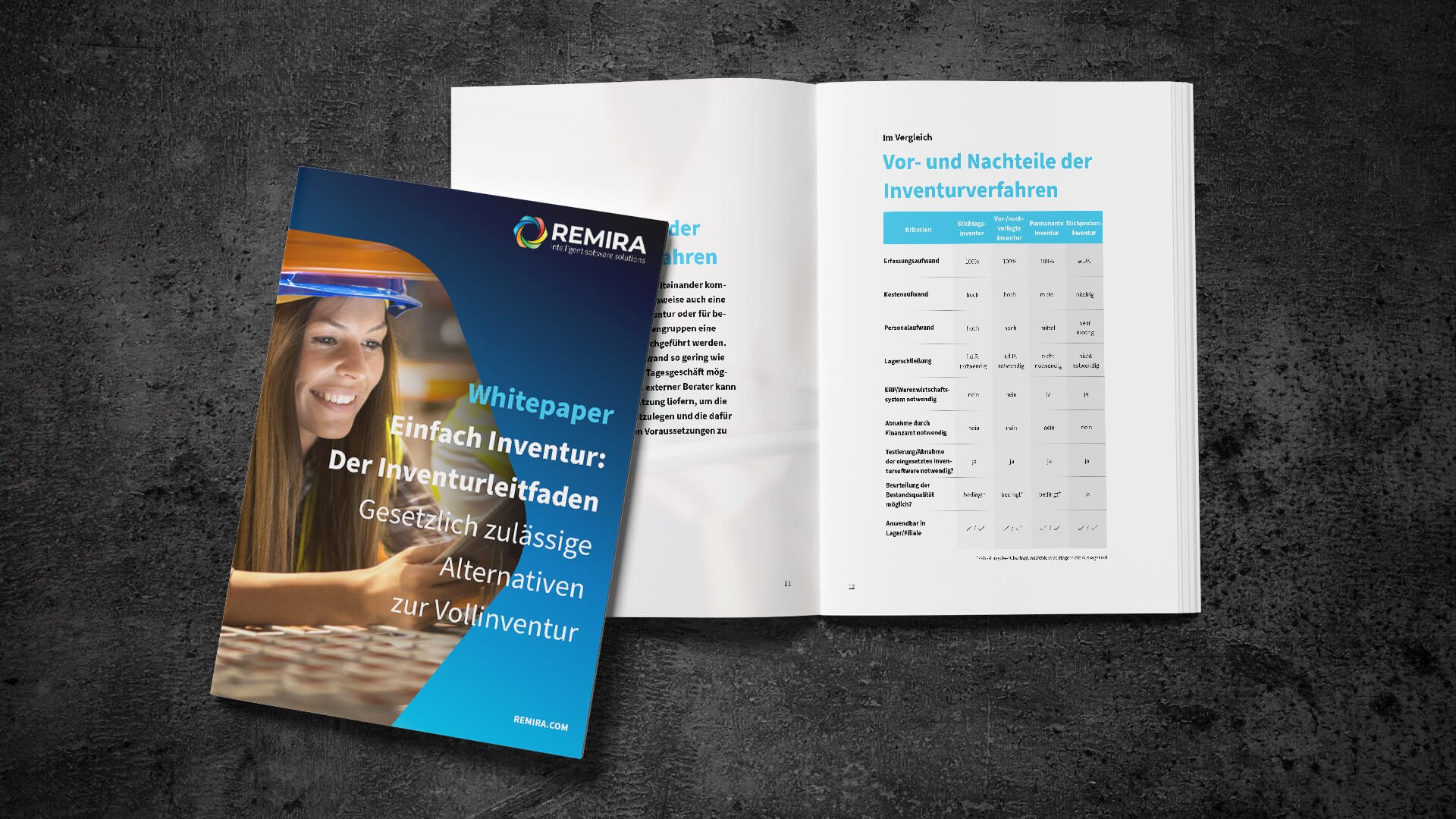
Easy Stocktaking: The Stocktaking Guide
Our whitepaper "Easy Stocktaking: The Stocktaking Guide" presents all legally permitted alternatives to full inventory and shows you how you can significantly reduce your inventory effort. In addition, you will learn how to determine your optimization potential and how sample stocktaking can be easily carried out in the cloud.
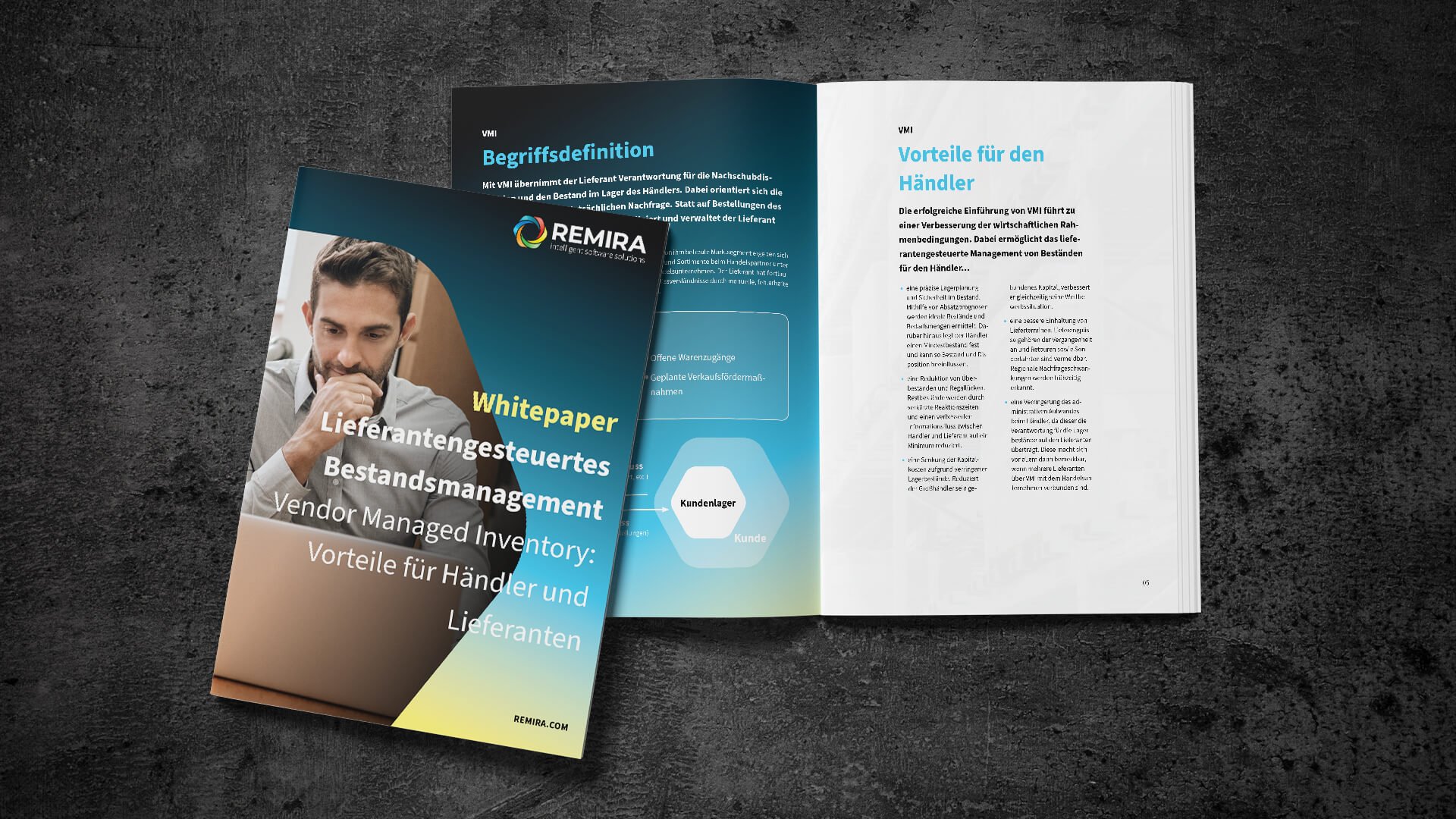
Vendor Managed Inventory: Advantages for Retailers and Suppliers
Our white paper "Vendor Managed Inventory: Advantages for retailers and suppliers" shows why vendor-managed inventory management is an important competitive factor, what potential suitable software solutions offer, and how the introduction of appropriate software works.
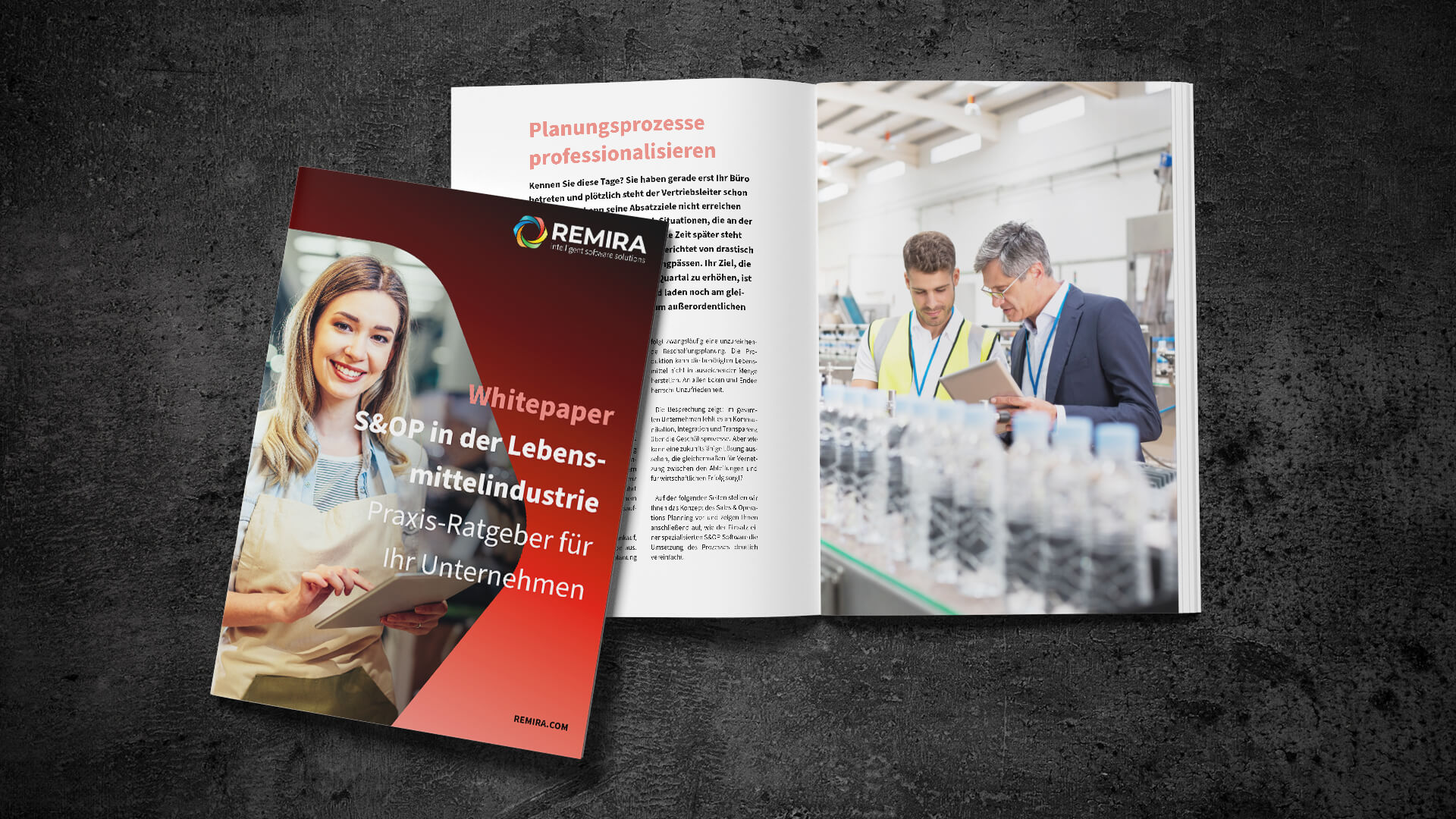
S&OP in the Food Industry
Our whitepaper "S&OP in the Food Industry" shows you how to combine and optimize your planning and decision-making processes in a unified process, gives you an insight into Sales & Operations Planning and demonstrates the benefits of using Sales & Operations Planning - with a focus on the food industry.
Alle Glossar-Begriffe