ABC-Analysis
Definition
The ABC analysis serves as economical analysis procedure. Part of the analysis is the evaluating and categorizing of customers, tasks, goods etc. into the classes A (high priority), B (medium priority) and C (low priority). In particular in the product management the ABC analysis finds frequent use. The ABC analysis is based on the Pareto principle (80/20 rule), named after the creator Vilfredo Pareto, which states that 80% of the happening or the results are due to 20% of the total time of the process. Simply put, the focus should be on what is most important. In a logistics context, this means that 20% of all items in the warehouse account for 80% of goods movements, and therefore it is important to focus on these items or to focus particularly on the warehouse movements of these items.
In many companies, most of the work is heaped on a few products and goods. Most inventory costs on a few expensive items and much of the revenue on a few sales. Therefore, resources, efforts and personnel should be directed to managing the most important and expensive items. They are responsible for a large percentage of the bottom line (Pareto principle).
Procedure: How is the ABC analysis carried out?
With a simple spreadsheet, it is possible to quickly create a simple ABC classification. For the start of the analysis it is very important that is clearly defined, what is to be analyzed and which data one needs for this. Afterwards the necessary data from accountancy, selling, camp etc. can be collected and sorted according to the information, which is needed for the ABC analysis. In the next step one sets borders, which determine, starting from when the value is sorted into which class.
For all objects, the stock and cost data are sorted in descending order of cost. Then the total costs are added and then the percentage that each product has of the total costs is calculated. The next step is to add the first rows until about 80% of the costs are identified. This should represent about 20% of the products. These products then form class A of the ABC classification. In this way one proceeds also for the B and C.
Overview classification:
- A goods: small quantity in the warehouse (20%), but the highest turnover rate and value. These goods must have an optimal stock, since they generate 80% of the turnover. Items are regularly counted and strictly controlled.
- B-goods: average share in value and quantity, as well as an average turnover rate, often minimum and maximum stocks are used here. The volume in the warehouse is about 30%. B category items are counted reasonably regularly and are reasonably controlled.
- C goods: largest share in the warehouse (50%), low stock value and little demand. Category C items are counted less frequently and controlled more carelessly.
The values can be determined for example on the basis the portions of the annual turnover, at the camp value or purchase value. In logistics an ABC analysis orients itself frequently also at the inventory turnover ratio.
Possible applications of the ABC classification in logistics
In logistics, the ABC analysis is often used to control the stocks or to determine the inventory value. Some products are more important than others and must be treated as such. For example, you can separate the items in stock according to criteria such as product sales, sales ratio, profit margin or inventory cost. In this case, the goods in the warehouse are divided into classes A, B, and C as usual, where the A group are the goods with the most importance (value, quantity, cost) and represent about 20% of the items or 80% of the profit, quantity, etc.). B-group items are of medium importance and represent about 30% of the items. The remaining 50% of the items should be in the C class.
XYZ-Analysis
Definition
XYZ analysis is a way to classify inventory items according to the variability of their demand or derived/forecasted consumption. XYZ analysis can be used to plan material requirements and inventory levels so that waste, production delays, or excessive inventory levels can be avoided. IXYZ analysis evaluates the ability to plan consumption and demand.
- X-goods - very low fluctuations: X-items are characterized by consistent sales over time. Future demand can be reliably forecast.
- Y-goods - some fluctuations: Although demand for Y-items is not constant, the variability of demand can be predicted to some degree. This is usually because fluctuations in demand are caused by known factors, such as seasonality, product life cycles, competitor actions, or economic factors. It is more difficult to accurately forecast demand.
- Z-goods - the greatest variation: demand for Z-items can fluctuate widely or occur sporadically. There is no trend or predictable causal factors, making reliable demand forecasting impossible.
Difference ABC/XYZ analysis
The ABC/XYZ analysis serves the better classification of the available stocks and/or the goods needed by the procurement. With the ABC analysis the individual articles are judged according to their portion (high value, middle value, small value) of the enterprise conversion. With the XYZ analysis the sales of durable articles, season articles and special offers can be prognosticated.
Combination of ABC and XYZ analysis in materials management
Combining ABC and XYZ analyses into an automated process gives companies a much more comprehensive view of their goods and customers' needs. Instead of three categories, ABC/XYZ analysis gives nine categories for classifying materials, goods and consumption. In the material management this analysis is therefore one of the most important aids for a lasting inventory optimization.
By the method a still more differentiated picture of the structure of the assortment of an enterprise results. The entire assortment can thus be tailored more specifically to the needs of the market. Even articles with unforeseen sales can be quickly identified with the help of the precise sales analysis and taken into account at short notice. The combination of both methods is an effective rationalization tool. It results in an optimal ordering rhythm for the products, so that excessive capital commitments and write-offs can be avoided.
By the combination of ABC and XYZ analysis a connection between the value portion of individual goods and the temporal need and/or consumption process of the respective article is manufactured. From this, important conclusions can be drawn for future assortment planning.
The nine classifications at a glance:
- XA, XB and XC
- YA, YB and YC
- ZY, ZB and ZC
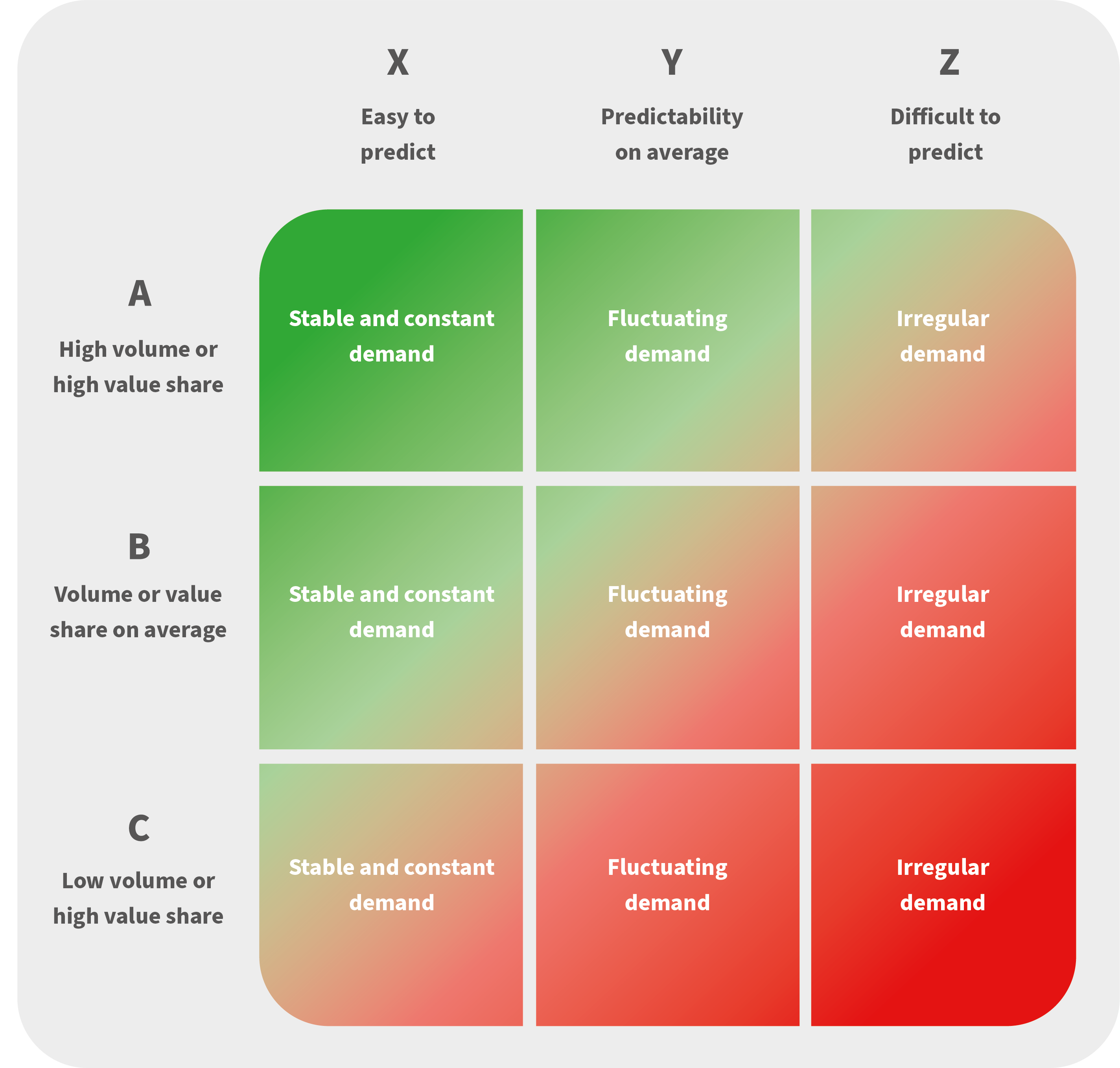
Objectives of ABC/XYZ analysis in logistics
The classification of individual goods is important for inventory management for several reasons. On the basis of the ABC analysis the conditions in the camp can be represented clearly and be reduced to the substantial. The analysis is not very complex and allows a quick and easy evaluation of all goods in the warehouse. In this way, companies achieve accurate information about the distribution of capital in the warehouse and can set appropriate priorities in warehousing and inventory management.
Objectives at a glance:
- Focus on the most important items
- Control and plan operational processes in a targeted manner
- Identify optimization potential
- Improve efficiency
- Control profitability within the company
In addition, classification enables supply chain managers to...
- ...identify warehouse items that pose the greatest business risks due to theft or damage and offer the greatest opportunities for sales,
- help warehouse managers and other supply chain professionals properly prioritize their time,
- enable warehouse managers to achieve near 100 percent inventory accuracy.
Monitoring inventory from A-Z
With the configurable ABC/XYZ service level matrix, safety stock levels can be dynamically controlled by item class. The higher the service level, the higher the probability of no inventory shortage. Forecast and sales data can also be viewed summed up for entire merchandise categories.
All in all, a combined ABC/XYZ analysis reduces monitoring costs many times over. After all, separate ABC and XYZ analyses mean twice the effort. The resources freed up can be put to good use elsewhere.
Derive findings and measures
After the classification of the individual positions was made, appropriate measures can be derived from the realizations. For example, more measures and more resources should be used for the items with high turnover than for C-products. The method is used to draw conclusions from the past, but the future should also play a role. It is therefore important to keep an eye on the development of the products and also to see potential in new products - even if they initially have only low sales.